2020. 3. 1. 16:25ㆍ카테고리 없음
Planners strive to optimize their project planning process and ensure high-quality automation documentation. When the maintenance of component libraries requires only a minimum effort, resources can be used more effectively. Pepperl+Fuchs now supports project planners with free EPLAN macros for our LB Remote I/O modules and Multi Function Terminals.Macros for EPLAN Electric P8 are available on specific model number pages of our website. The macros allow users to natively integrate the LB Remote I/O modules and Multi Function Terminals in their planning and documentation. Prolonged waiting time is not an issue because the CAD and CAE data for the respective product is immediately available.
Working with datasheets always bears the risk of transfer and interpretation errors. By using the macros, this risk is eliminated as is the time consuming manual creation of symbols. Planning projects are quickly completed.
Eplan Macros Siemens Download
Impulse Withstand Voltage as High as 10kV with 4kV Dielectric Strength: Ideal for Power Supply Switching. Input and output (between coil and contacts) are completely separated, with impulse withstand voltage of 10,000 V.
Insulation distance of 8 mm min. Between coil and contacts satisfies the VDE Standard C/250 insulation requirements, and conforms to Electrical Appliance and Material Safety Law with dielectric strength of 4,000 VAC min.
Standard model conforms to UL/CSA standards. VDE standard approved models are also available. Consult your Omron sales representative for availability.
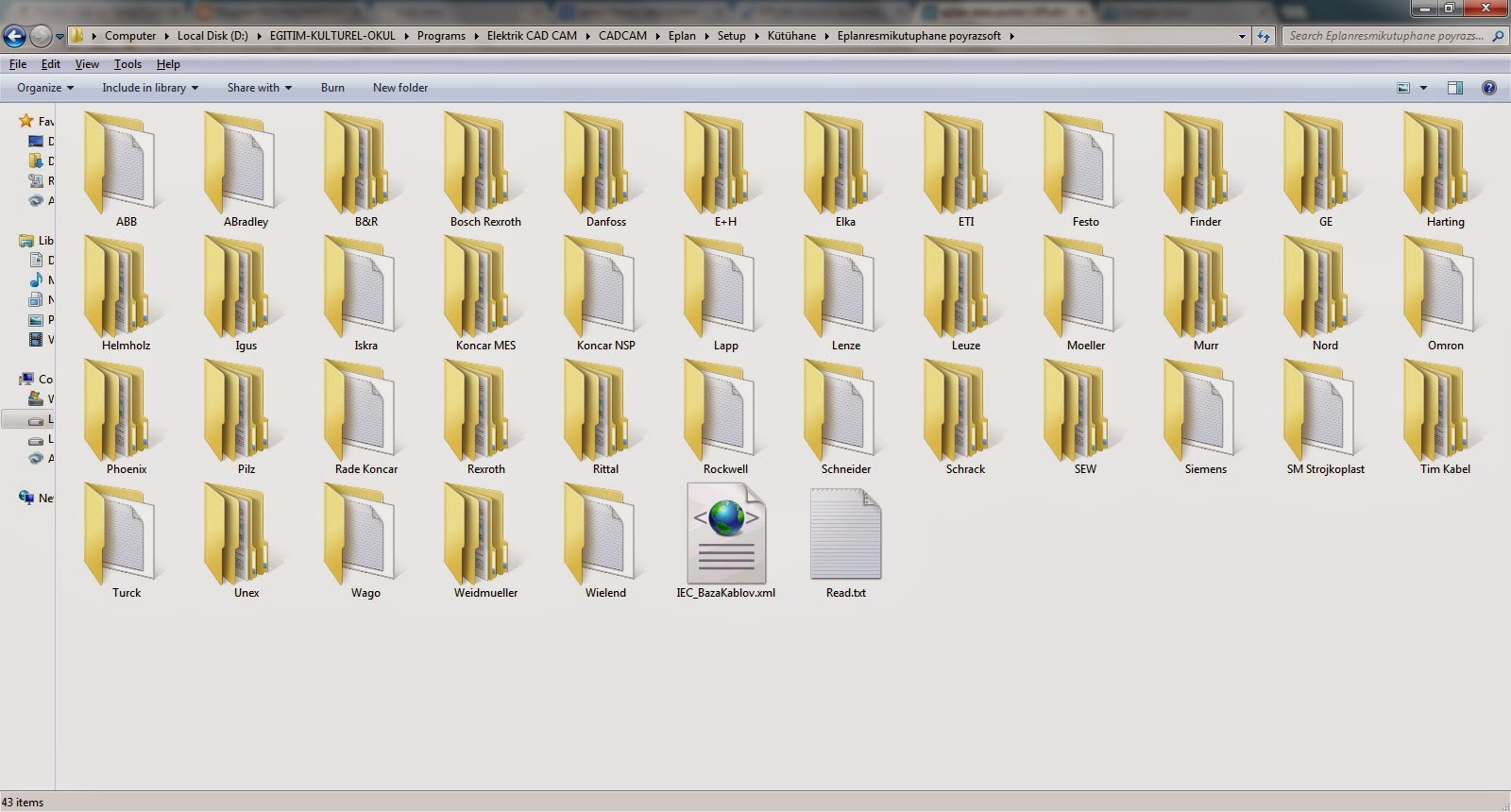
SPST-NO (1a) types conform to TV-8 rating, and DPST-NO (2a) types conform to TV-5 rating. Full-wave bridge rectifier compatible models are also available. Rated voltageRatedcurrent(mA)Coilresistance( Ω)Mustoperatevoltage(V)Mustreleasevoltage(V)Max.voltage(V)Powerconsumption(mW)% of rated voltage12 VDC66.718080%max.10%min.130%(at 23°C)Approx. 800 mW24 VDC VDC812,500Note:1.The rated current and coil resistance are measured at a coil temperature of 23ºC with a tolerance of ±15%.2.Operating characteristics are measured at a coil temperature of 23ºC.3.The “Max. Voltage” is the maximum voltage that can be applied to therelay coil.Contact Ratings.
Omron Eplan Macromolecules
ItemSPST-NO (1a)DPST-NO (2a)Resistive load(cos φ = 1)Inductive load(cos φ = 0.4)Resistive load(cos φ = 1)Inductive load(cos φ = 0.4)Contact materialAg-Alloy (Cd free)Rated load15 A at 250 VAC15 A at 24 VDC10 A at 250 VAC7.5 A at 24 VDC10 A at 250 VAC10 A at 24 VDC7.5 A at 250 VAC5 A at 24 VDCRated carrycurrent15 A10 AMax. Switchingvoltage250 VAC, 125 VDCMax.
Switchingcurrent15 A10 ACharacteristicsContact resistance.130 mΩ max.Operate time20 ms max.Release time5 ms max.Max. Operating frequencyMechanical18,000 operations/hrElectrical1,800 operations/hrInsulation resistance.2100 MΩ min. (at 500 VDC)Dielectric strengthBetween coil and contacts4,000 VAC, 50/60 Hz for 1 minBetween contacts of the same polarity1,500 VAC, 50/60 Hz for 1 minBetween contacts of different polarities2,000 VAC, 50/60 Hz for 1 minImpulse withstand voltageBetween coil and contacts10,000 VVibration resistanceDestruction10 to 55 to 10 Hz, 0.75 mm single amplitude(1.5 mm double amplitude)Malfunction10 to 55 to 10 Hz, 0.75 mm single amplitude(1.5 mm double amplitude)Shock resistanceDestruction1,000 m/s 2Malfunction150 m/s 2DurabilityMechanical5,000,000 operations min. (at 18,000 operations/hr)Motor load100,000 operations min.(rated load, at 1,800 operations/hr)Failure rate (P level) (reference value).3100 mA at 5 VDCAmbient operating temperatureOperating: -25ºC to 55ºC (with no icing or condensation)Ambient operating humidityOperating: 5% to 85%WeightApprox. 29 gNOTE:The above values are initial values.1.The contact resistance was measured with 1 A at 5 VDC with a fall-of-potential method.2.The insulation resistance was measured with a 500 VDC Megger Tester applied to the same parts as those for checking the dielectric strength.3.This value was measured at a switching frequency of 120 operations/min.
Correct Use ●Mounting.When mounting more than two Relays on a PCB, keep the gap as shown in the following figure.No specified mounting direction.Not compatible with sockets.There is the current-carrying metal part on the coil terminal.Do not mount to the PCB with patterned metal surface. ●Other Precautions.This Relay is suitable for power load switching of motors, transformers, solenoids, lamps, heaters, etc.Do not use the G4W to switch micro loads less than 100 mA, such as in signal applications.